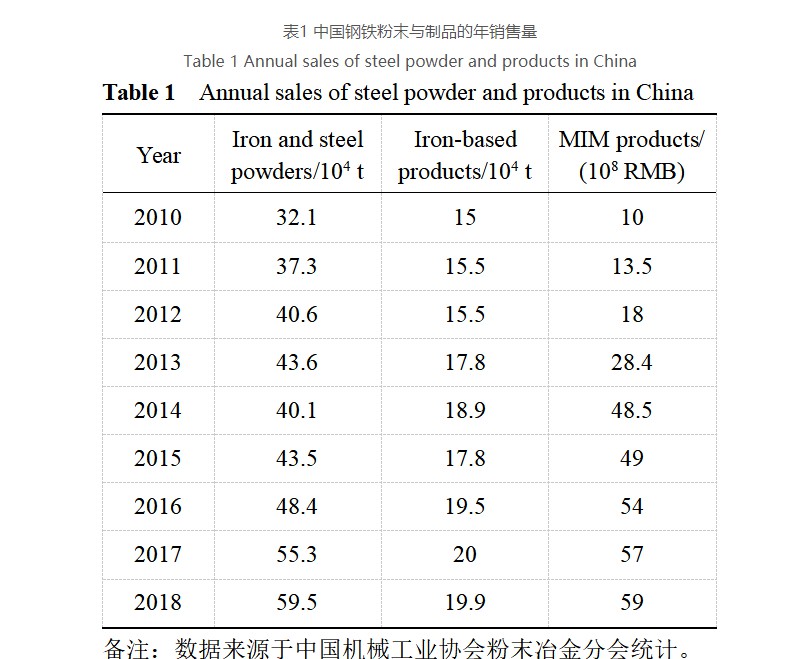
“庆祝新中国成立70周年”特刊系列栏目,邀请领域内顶尖学者执笔撰稿,记录有色金属工业和有色科技发展历程的标志性事件、节点、人物、存在的问题及未来的展望,涉及我国有色金属行业的地质、采矿、选矿、冶金、材料等领域,全方位立体化展现中国有色金属领域科技创新的重要成就和重大进展,见证中国有色金属工业70年从成长到壮大的辉煌历程。
黄伯云,男,1945年11月24日生,湖南省南县人,汉族,天富代理中南大学教授,博士生导师,中国工程院院士,《中国有色金属学报》主编。
黄伯云1969年毕业于中南矿冶学院(现为中南大学)粉末冶金专业,1980—1986年留学美国爱阿华州立大学及AMES国家实验室并获得硕士、博士学位;1986年8月至1988年5月在美国田纳西大学及橡树岭国家实验室从事博士后研究工作, 1988年5月归国。回国后一直在中南大学(含原中南矿冶学院、中南工业大学)工作,历任教授、博士生导师、所长、副校长、校长。黄伯云1999年当选中国工程院院士,2007年当选第三世界科学院院士,曾任国家973计划首席科学家,“十五”国家863计划新材料领域专家委员会主任,中国科学技术协会全国委员会副主席,湖南省科学技术协会主席,中国材料研究学会理事长,中国共产党第十六、十七次全国代表大会代表,第十一届全国政协委员,第十二届全国人民代表大会常务委员会委员。
黄伯云主要从事新材料研究,在先进复合材料、高性能摩擦材料、高温结构材料、粉末冶金新材料等领域完成了一系列技术发明与创新,获得国家科技成果奖4项,国家教学成果奖二等奖2项。其中,高性能炭/炭航空制动材料的制备技术荣获2004年度国家技术发明一等奖, 结束了该奖项连续六年空缺的历史;他还获得了何梁何利科学与技术进步奖、留学回国人员成就奖、以及国家中青年有突出贡献专家、全国杰出专业技术人才、全国国防科技工业系统先进工作者、全国优秀共产党员、全国劳动模范。
黄伯云是粉末冶金国家重点实验室首任主任,粉末冶金国家工程中心、轻质高强材料国防科技重点实验室创始人,领导创建了博云新材上市公司以及粉末冶金研究院的多家学科性公司。担任粉末冶金研究院(所)院长(所长)以来,提出了建立大团队、构建大平台、承担大任务、取得大成果、作出大贡献的学科建设与发展思想,使粉末冶金学科建设和人才培养得到了快速发展,受到了国家各级领导的高度重视。自2005年来,两届中央领导相继到粉末冶金国家重点实验室视察、指导。2013年11月4日,习近平总书记视察粉末冶金国家重点实验室,听取了黄伯云院士关于粉末冶金学科科技创新、服务国家重大战略情况汇报后,对粉末冶金学科的创新发展给予了高度肯定。
摘要
本文概述了建国70年以来中国粉末冶金材料的发展状况,包括铁基粉末冶金材料、硬质合金、粉末冶金磁性材料、粉末冶金高温合金等先进粉末冶金材料,以及国内外在粉末增材制造、放电等离子烧结等粉末冶金先进成形领域的发展状况,为现代粉末冶金材料及技术的发展提供了新的思路。
引言
粉末冶金作为一种既古老又充满活力的先进材料制备和成形技术,天富代理起源于古代陶瓷制备技术和炼铁技术,为人类社会的发展做出了重要贡献。18世纪中叶,粉末冶金制铂技术在欧洲的兴起,开启了古老粉末冶金技术的复兴时代。直至1909年,粉末冶金法延性钨的问世标志着近现代粉末冶金时代的来临。一百多年来,粉末冶金技术蓬勃发展,各种重要新型材料和关键性制品不断涌现,成为当今国民经济和科学技术不可或缺的重要工程技术之一。迄今,粉末冶金技术已发展成为材料科学和工程领域中最具有发展活力的重点研究方向之一。
粉末冶金是以金属粉末(或金属粉末与非金属粉末的混合物)为原料,经成形和烧结过程制造金属材料、复合材料以及多种不同类型制品的工艺方法。粉末冶金技术所带来的重要变革主要体现在以下两个方面:一是开发新型材料和关键制品的先进技术。1909 年开发出的粉末冶金延性钨丝,为人类社会带来了光明。1923 年硬质合金的问世,将金属切削加工效率提高几十倍甚至上百倍,为切削加工、采掘钻探以及其它加工业带来革命性变革。20 世纪 30 年代以来,基于粉末冶金技术开发的难熔金属、电触头材料和磁性材料(包括稀土永磁材料),为电气化系统和通讯设备提供关键器材和元件。二是生产高性能金属机械零件的先进成形工艺。由于粉末冶金技术能实现材料的近净成型,具有原材料利用率高(约95%)、生产效率高、节能环保的优势,能够直接生产形状复杂、高精度的高性能粉末冶金产品。世界范围内的粉末冶金机械零件产业发展迅速,确立其作为现代制造业的重要组成地位。
本文将着重介绍现代粉末冶金技术领域主要材料体系(铁基、硬质合金、磁性材料和粉末高温合金)和新兴成形技术(增材制造、放电等离子烧结等)的最新进展。
铁基粉末冶金材料
铁基粉末冶金材料是以铁元素为主,添加C、Cu、Ni、Mo、Cr、Mn等合金元素形成的一类钢铁材料。其中,粉末冶金低合金钢中合金元素之和一般在5%(质量分数)以下,已发展形成Fe-Cu-C、Fe-Ni-C、Fe-Ni-Cu-C、Fe-Cr-Cu-C、Fe-Mo-Ni-Cu-C等多个系列;粉末冶金高合金钢有粉末不锈钢和粉末高速钢两大类。铁基制品是粉末冶金行业生产量最大的一类材料,在一定程度上代表一个国家粉末冶金技术水平。下面介绍铁基粉末及其制品的发展概况。
(一) 铁基粉末
粉末冶金铁基材料和制品所使用的粉末主要包括纯铁粉、铁基复合粉末、铁基预合金粉末等。我国钢铁粉末的制备技术不断发展,现已开发出还原法、羰基法、电解法、超高压水雾化、热气体雾化、水汽联合雾化、粘结扩散、预合金化、预混合等制备技术。这些技术的开发丰富了我国铁基粉末品种和质量。我国已开发出应用铁精矿粉生产还原粉、高压缩性铁粉(600 MPa压制密度达到7.24 g/cm3)、无偏析混合粉、水雾化预合金钢粉(Fe-Mo等)、扩散型合金钢粉(Fe-Ni-Mo-Cu等)、易切削钢粉(添加MnS)、烧结贝氏体钢粉、电焊条粉、磁性材料用铁粉、冶金炉料用铁粉、化工行业用铁粉等多种产品,满足了市场需求。2017年莱钢集团粉末冶金有限公司建成了年产9万t高性能水雾化铁粉的自动化生产线,我国已具备了在一定区域内与国际企业竞争的实力。我国2010~2018年钢铁粉末销量年平均增速约为10%(见表1),2018年销量达59.5万t,其中年产超万吨的11家钢铁粉末公司的总产量已占国内总产量的93%,说明钢铁粉末生产的规模化优势正在显现。然而,目前国内铁粉行业的生产与下游行业需求处于不平衡的状态,低档次铁粉产量大于需求,而高档铁粉却依然处于供不应求的局面,其中预混合钢粉、预合金钢粉和扩散型合金钢粉等仍主要依赖进口,钢铁粉末的质量、品种及稳定性等仍与国外知名生产企业(如瑞典Höganäs公司、加拿大魁北克金属粉末公司 (QMP)、美国Höeganäes公司、日本JFE公司、日本神户制钢公司等)存在一定的差距。
表1 中国钢铁粉末与制品的年销售量
Table 1 Annual sales of steel powder and products in China
(二)P/M铁基制品
常规压制/烧结技术一般可生产密度6.4~7.2 g/cm3的铁基制品,用于汽车、摩托车、家电、电动工具等行业,具有减震、降噪、轻量化、节能等优势。建国以来,我国铁基制品行业得到了国家机械部的高度重视,从无到有艰难创业。改革开放后,在汽车、摩托车、机械制造等行业的带动下,铁基制品行业快速发展,成型压机、模具设计及制造、烧结及热处理炉等相关设备制造和配套能力不断增强。
随着中国制造的发展,对铁基制品的密度、强度、精度等指标提出了更高的要求。铁基材料的高致密化和强化技术研究受到重视,相关技术包括高速压制、液相烧结、微合金化等。目前国内部分铁基粉末冶金零件企业的核心技术已将温压、粉末热锻、表面滚压致密化、生坯可加工、复压复烧、热等静压等应用于高致密度、高精度、高复杂度零件的制备。例如,烧结后的铁基齿轮经过滚压致密化处理,与齿部接触的表面几乎达到全致密。齿轮的尺寸精度和表面接触疲劳强度大大提高,可代替锻造齿轮。应用生坯可加工技术可以低成本生产出常规压制/烧结难以制备的复杂形状的铁基零部件。经过多年的发展,中国已成为亚洲最大的铁基粉末冶金制品生产国,产生了东睦新材料集团股份有限公司等龙头企业。据中国机械工业协会粉末冶金分会统计(见表1),2018年中国粉末冶金铁基制品实现产量19.94万t。近11年的数据分析平均复合年增长率约为10%,但我国铁基粉末冶金高端产品和企业规模还有待突破。
(三) 粉末注射成形(MIM)铁基制品
金属粉末注射成形技术(MIM)是以金属粉末为原料,借助塑料注射成形工艺制造形状复杂的小型金属零部件。20世纪90年代,中南大学等单位在国家高新技术研究发展计划等项目的支持下开始MIM材料和技术的研究,发明了环保型的粘结剂和快速溶剂脱脂技术、发展了流变学理论指导喂料设计,在此基础上先后开发出Fe-Ni、不锈钢等铁基材料的系列注射成形制备技术用于枪械、医疗器械等零部件的制造。
国内MIM产业的发展经历了十多年的艰难探索,终于在手机行业的应用取得了重要突破,2010年后MIM产业获得了快速发展(见表1),据中国钢构协会粉末冶金分会不完全统计,中国的MIM公司已有140家以上,主要分布于珠三角、长三角和京津地区。2017年国内MIM行业产值达到54亿元,江苏精研科技股份有限公司也在2017年成功在新三板上市,年产值约10亿元。
MIM材料方面,目前70%应用的材料为不锈钢,20%为低合金钢材料。76%产品为3C产品,其中手机65.7%, 计算机4.9%,可穿戴设备6.9%。MIM技术在手机、计算机等行业用量逐年增加,目前苹果、三星、华为、VIVO、OPPO等手机、联想计算机都大量采用MIM零件,中国手机生产量占全球约80%,手机巨大的年产量和快速的更新换代为MIM技术提供了巨大的发展空间。如手机SLM卡箍、照相机环等。随着手机超薄化、智能化及大屏化的发展,MIM技术还会大有作为。
(四)铁基粉末冶金材料的发展趋势
粉末冶金新技术正在向粉末复合化、成形高精度化、烧结高热效率化和后加工与其他技术融合等方面进行技术革新。
1) P/M铁基制品的发展方向:
开发高性能、高稳定性的钢铁粉末原材料,开发高密度、高强度、高精度的铁基制品制备技术,发展自动化和数字化生产技术和装备。目前东睦新材料股份有限公司和扬州宝来得等公司正在大力推行自动化和数字化生产。
2) MIM技术和产品的发展趋势:
开发尺寸和质量更大的复杂零部件的生产技术(50~200 g的产品);开发更多的微注射成形产品;开发共注射成形技术,实现零件和表面处理同步完成;与增材制造技术相互补充;开拓在汽车、医疗、能源等领域的新产品,摆脱过度依赖3C产品的现状;缩短研发周期;提高精度;降低成本。
3) 增加铁基粉末冶金在医疗器械、精密制造、军工、航空航天等高端应用领域的应用比重,提高产品的附加价值是铁基粉末冶金制品另一发展方向。
硬质合金
硬质合金是以过渡族难熔金属碳化物或碳氮化物作为主体成分的粉末冶金硬质材料。因具有较好的强度、硬度、韧性匹配性,硬质合金主要用作切削刀具、采掘工具、耐磨零件以及顶锤、轧辊等,广泛应用于钢铁、汽车、航空航天、数控机床、机械工业模具、海洋工程装备、轨道交通装备、电子信息技术产业、工程机械等装备制造加工和矿产、油气资源采掘、基础设施建设等行业领域[10]。2015年欧洲粉末冶金工业协会发布的2025欧洲粉末冶金发展战略路线图中明确指出:硬质合金是现代制造工业的脊梁。
表2列出了近年来中国钨业协会硬质合金分会等提供的中国硬质合金的企业数量、产能、硬质合金总产量和总出口量。由于需求的稳步增长和行业持续的科技进步,中国硬质合金产业呈现良好的持续发展态势。中国硬质合金已经形成以中钨高新、厦门钨业等上市公司为代表的具有国际竞争力的硬质合金产业集群,拥有粉末冶金国家重点实验室、硬质合金国家重点实验室、国家钨材料工程技术研究中心等公共创新平台。
表2 2010~2018年中国硬质合金工业数据
Table 2 Cemented carbide industry data in China (2010−2018)
(一)超细晶和超粗晶硬质合金
作为世界钨资源大国,中国硬质合金总产量的世界占比已经超过40%。在世界硬质合金科技发展史上,中国制造标志性技术成果的典型代表是紫钨制备技术。20世纪90年代末期,中国硬质合金行业自主研发的紫钨制备产业化技术属于国际首创。紫钨制备技术是一种以紫色氧化钨(WO2.72)为原料制备后续制品的工艺技术。采用紫钨工艺制备超细或纳米钨粉和碳化钨粉具有生产效率高、成本低、产品质量与质量稳定性可控度高等特点,已成为中国生产超细或纳米钨粉、碳化钨粉和超细晶硬质合金的主流工艺。2011年,GB/T 26725《超细碳化钨》国家标准正式发布,其中FWCN30牌号WC粉末的比表面积>7.60 m2/g,比表面积平均径<50 nm。随着超细晶硬质合金晶粒生长抑制机理研究的突破和压力烧结工艺的推广应用,超细晶硬质合金的生产技术已经成熟,目前中国已经能够批量生产具有世界先进水平的平均晶粒度约0.2 μm的高品质超细晶硬质合金。据2018 年中国钨业协会硬质合金分会发布的全国硬质合金行业《统计年鉴》报道,26家中国硬质合金企业2018年共生产整体刀具用晶粒度<0.6 μm超细晶硬质合金棒材11079.7 t,同比增长22.46%;其中厦门金鹭特种合金有限公司产量为4045.3吨,占比为36.5%。厦门金鹭特种合金有限公司含Co质量分数为12%的GU25UF超细晶硬质合金抗弯强度平均值已达5000 MPa以上的水平。
目前,中国高温还原、高温碳化制备高纯超粗晶WC粉末的制备技术已经得到推广应用,中国硬质合金企业生产的合金晶粒度5~10μm的超粗晶硬质合金已广泛应用于路面铣刨、采煤、盾构施工以及冷镦模具等。
(二)硬质合金材料的发展趋势
1 集成计算材料工程
采用基于第一性原理计算、CALPHAD方法、相场模拟和有限元模拟等计算模拟的集成计算材料工程,可极大地提高难熔金属与硬质合金领域新材料的研发效率。继国际知名企业Sandvik以后,中南大学杜勇教授团队开发了包含 C-Co-Cr-W-Ta-Ti-Nb-N 等元素的难熔金属与硬质合金热力学和动力学数据库。采用该数据库,可以计算各种组元的相平衡,获得各种物相的热力学性质和溶解度信息,模拟合金中元素和相的分布状态,可为材料与工艺设计奠定理论基础。
2 硬质合金微结构调控
过渡族金属碳化物是硬质合金中最常见的添加剂,可用于调控硬质合金微观组织结构与性能。添加剂在硬质合金中赋存状态的研究是硬质合金材料强化机理和碳化钨晶粒生长抑制机理研究的基础,也是硬质合金材料与工艺设计的基础。早在1972年,日本学者HAYASHI等就对WC-Co硬质合金中WC晶粒生长抑制进行了系统研究。研究结果表明,在1400 ℃烧结温度下,当金属碳化物的添加量达到其在液相中的饱和溶解度时,其对碳化钨晶粒生长抑制效果的排序如:VC>Mo2C>Cr3C2>NbC>TaC>TiC>ZrC/HfC。在随后的30年内,硬质合金中碳化钨晶粒生长抑制机理的研究一直处于不断探索中。
研究结果表明,VC、Cr3C2在硬质合金中的主要作用是抑制合金中WC晶粒生长,其中Cr3C2还具有改善合金耐腐性能的作用;TaC、NbC的主要作用是提高合金的红硬性和抗热冲击性能;TiC的主要作用是改善合金在高温下的化学稳定性、阻碍高温下铁基(钢铁)被加工件与硬质合金切削刀具之间的扩散行为;Mo2C的主要作用是改善粘结相对含Ti(C,N)的润湿性。然而长期以来,合金添加剂改善硬质合金性能的机理尚无定论。
1993年EGAMI等首次报道了在WC-Co-VC合金中WC/β(钴基固溶体粘结相)相界处存在V的偏析现象。随后,过渡族金属碳化物添加剂在WC-Co硬质合金晶界和相界的偏析行为以及在碳化钨和钴相中固溶行为的研究不断深入。过渡族金属碳化物的界面偏析对合金界面特性以及与此相关的晶粒特性(晶粒形貌、晶粒度、晶粒分布等)以及合金的综合性能具有较大影响。过渡族金属碳化物添加剂的溶解和偏析行为与硬质合金中碳化钨晶粒生长及其抑制机理以及合金性能的影响机理密切相关。基于高分辨透射电镜和三维原子探针的实验观察分析,不但使WC晶粒生长抑制机理的研究取得了突破性进展,也使添加剂在硬质合金中作用机理与合金性能影响机理的研究取得了突破性进展。过渡族金属碳化物添加剂在硬质合金中碳化钨/碳化钨晶界与碳化钨/β相界均存在偏析行为,在碳化钨硬质相与合金粘结相中均存在固溶行为,通过合金添加剂在硬质合金中作用行为的调控,可实现对硬质合金微观结构与性能的有效调控。
粉末冶金磁性材料
粉末冶金磁性材料指用粉末成型和烧结的方法制备的磁性材料,可分为粉末冶金永磁材料和软磁材料两大类。永磁材料主要包括钐钴稀土永磁材料、钕−铁−硼系永磁材料、烧结铝镍钴永磁材料、铁氧体永磁材料等。粉末冶金软磁材料主要包括软磁铁氧体和软磁复合材料等。粉末冶金法制备磁性材料的优势在于,能制备单畴尺寸范围的磁性微粒,在压制过程中实现磁粉的一致取向,直接制出接近最终形状的高磁能积磁体,尤其是对于难加工的硬脆磁性材料而言,粉末冶金法的优越性更加突出。
(一)钐钴(Sm-Co)稀土永磁材料
钐钴稀土永磁材料包括两大类,即SmCo5永磁合金和Sm2Co17型永磁合金,其中,Sm2Co17型永磁合金具有较为优异的综合磁性能,在工业上获得了较为广泛的应用,包括微波通讯、电机工程、微波器件、测量仪表等静态或动态磁路。Sm2Co17型永磁合金的磁性能来源于其特有的胞状/片状纳米复合结构,如图1所示。胞内主要由富Fe的Sm2(Co,Fe)17菱方相构成,胞壁由富Cu的Sm(Co,Cu)5六方相构成,片状相叠加于胞状结构之上。该合金的矫顽力机制为畴壁钉扎型, Cu富集于胞壁相有利于该相磁晶各向异性能的降低,增大Sm2(Co,Fe)17相与Sm(Co,Cu)5相之间的畴壁能差,并导致矫顽力增大。
一直以来,研究者都致力于通过改善合金成分和制备工艺,来提高材料的室温和高温磁学性能。HORIUCHI等采用了多级热处理工艺,在Sm(CobalFe0.35Cu0.06Zr0.018)7.8发现磁体的平均晶粒尺寸从44.1 μm增加到59.1 μm,最大磁能积达到281.78 kJ/m3。SONG等采用分级降温时效工艺,制备了富Fe的Sm(Co0.65Fe0.26Cu 0.07Zr0.02)7.8磁体。在时效分级降温阶段,磁体的剩磁(Br)几乎保持不变,内禀矫顽力(Hcj)从1.646×106 A/m逐渐增大到2.505×106 A/m,在400 ℃淬火冷却到室温后,磁体的最大磁能积((BH)max)达到255.36 kJ/m3。另一方面,该类材料的高温磁性能一直是研究的重点。用重稀土元素取代Sm2Co17型永磁体中的部分Sm可以制备出具有低磁感温度系数的永磁材料Sm1xDyx(Co0.695Fe0.2Cu0.08Zr0.025)7.2、Sm0.8Re0.2 (CobalFe0.22Cu0.06Zr0.03)7.4 (Re=Gd, Er)。通过降低Fe含量,增加Co含量可制备出使用温度达550 ℃的高温磁体。YU等通过调整Fe和Cu含量,在500 ℃获得Br=0.765 T,Hcj=5.013×105 A/m,(BH)max=98.704 kJ/m3的SmCo磁体。目前,国内钐钴企业目前已经能够普遍生产磁能积为28~30 MGOe的SmCo磁体。1998年钐钴稀土永磁的年产量约为105 t,到2018年我国钐钴磁体产量已增加至2500 t。
(二) 烧结钕−铁−硼(Nd-Fe-B)系稀土永磁材料
具有优异磁性能的烧结Nd-Fe-B系稀土永磁材料是第三代稀土永磁材料,被称为“磁王”。烧结Nd-Fe-B系永磁材料主要由Nd2Fe14B主相、富Nd相、富B相和少量的稀土氧化物组成,按成分可以分为三元Nd-Fe-B永磁材料和以Pr、Dy、Tb取代部分Nd,以Co、Al、Cu、Nb、Gd等取代部分Fe而形成的三元以上的永磁体;按磁性能可分为矫顽力不同的N型、M型、H型、SH型、UH型、EH型和AH型永磁体。该材料被广泛应用于电动机、发动机、音圈马达、磁共振成像仪、通讯、控制仪表、音响设备等方面,尤其是近年来在快速发展的风力发电、 新能源汽车、变频空调等领域的应用更推动了该材料的进一步发展。
烧结Nd-Fe-B系稀土永磁材料采用典型的粉末冶金工艺制备,包括合金熔炼、制粉、磁场压制成型、烧结、热处理及表面处理等。速凝铸造工艺、氢气破碎、气流磨制粉、晶界扩散等工艺技术的采用大幅提高了钕铁硼磁体的磁性能。近年来,利用高丰度低价格 La、Ce、Y及其混合稀土替代Nd-Fe-B中的一部分Pr、Nd不仅可降低原料成本,还可实现稀土资源综合利用,逐渐受到人们的关注。一系列的富含稀土La、Ce、Y的Nd-Fe-B系稀土永磁材料在国内外的大量实验室、科研院所或生产企业被开发出来,例如:(Nd1−xCex)30(FeTM)balB、(Nd0.75Ce0.25)30.5FebalAl0.1Cu0.1B、(Pr71Nd9Ce20)70Cu30、NdyFe(86−y−x)B14Mx等。这些材料不同于传统Nd-Fe-B合金的单一主相,具有双主相结构。日本东北大学 HOMMA等报道了5%Ce(质量分数)替代磁体的研究工作,成功制备出Br为13.5 kGs、Hcj为10.2 kOe 的磁体。但是,在类似轻稀土元素替代烧结磁体的研究工作中,La、Ce、Y替代Pr、Nd量普遍较低,尚未实现高替代量,还有待进一步的研究工作开展。
图1 Sm2Co17磁体胞状组织:(a) 结构示意图;(b) TEM图
Fig. 1 Structure of Sm2Co17 magnetic materials: (a) Schematic illustration; (b) TEM image
20世纪90年代前,全球钕铁硼材料的生产企业主要集中在日本、欧美等发达国家。近30年我国的钕铁硼材料产业飞速发展,1990年,我国烧结钕铁硼材料产量仅占世界毛坯总产量的10.8%,约为180 t;2018年,我国烧结钕铁硼毛坯产量约15.5万t,是全球烧结钕铁硼产量最大的国家。据统计,目前我国钕铁硼材料生产企业有200多家,主要分布在沪浙地区、京津地区和山西地区等。
(三)永磁铁氧体
钡铁氧体和锶铁氧体是目前应用最广泛的永磁铁氧体材料,具有较高的磁能积、矫顽力和剩磁以及宽的磁滞回线,广泛应用于汽车电机、电动工具、家用电器、办公自动化设备等领域。目前,永磁铁氧体的生产厂家主要分布在中国、日本、美国和部分欧洲国家,其中日本TDK公司开发的FB12系列产品的磁性能已经接近理论值。
高性能的永磁铁氧体须满足的条件为:具有高的饱和磁化强度和高的磁晶各向异性。由此,人们研究开发出了离子取代、共混复合等技术,通过调节晶体结构来调控材料的各向异性和磁化强度。比如,WAKI等开发出了La-Co共同取代的M型锶铁氧体、LI等研究了Co-Ti原子等比例取代Fe原子的Ba(CoTi)xFe12−2xO19铁氧体、XIA等制备了SrFe12O19/CoFe2O4复合材料、LI等制备了SrFe12O19/Fe-B复合材料。这些工作为高性能永磁铁氧体提供了新的发展方向。同时,在永磁铁氧体的制粉过程中,将原料磨细来增加单畴粒子的体积分数,可以提高永磁铁氧体的性能。国内外生产企业开发出了分级研磨或者循环研磨技术,将原料球磨到1μm以下,明显提高了材料的磁性能。另外,通过晶粒生长抑制剂抑制晶粒异常长大,增大单畴离子的比例,同样提高永磁铁氧体的磁性能。另外,提高取向度和烧结密度,同时控制晶粒大小均匀也是提高永磁铁氧体性能的有效途径。
永磁铁氧体由于不含有高价值金属元素,如Ni、Co以及稀土等,因此成本较低,在工艺品、吸附件、玩具、电机、传感器、医疗器械、扬声器等设备方面的应用具有较大优势。作为世界上最大的磁性材料生产国家,我国的永磁铁氧体产量占全世界70%左右,如图2所示。国内较大的永磁铁氧体的生产厂家有东磁集团、领益智造(原江粉磁材)和北矿磁材等。
图2 2011~2017年全球和中国的永磁铁氧体产量(来源:中国电子元件行业协会磁性材料与器件分会)
Fig. 2 Global and Chinese production of permanent magnet ferrite materials (2011−2017) (Source: China Electronic Components Association, Magnetic Materials and Devices Branch)
(四)软磁铁氧体
软磁铁氧体包括尖晶石结构的Mn-Zn低频铁氧体、Ni-Zn高频铁氧体和平面六角晶系的磁铅石型超高频软磁铁氧体,其电阻率远大于金属磁性材料,可抑制涡流的产生,主要用于消费类电子产品中。软磁铁氧体发展方向主要是制备具有高饱和磁通密度、高磁导率和低损耗的软磁铁氧体。
软磁铁氧体通常采用传统的氧化物粉末冶金烧结法来制备。为了提高材料致密度,BARBA等在Ni-Zn-Cu系铁氧体中,先以较快的速度升到较高的温度,实现样品快速致密化,然后再降至较低的温度进行保温,获得了较高的密度。PETRECCA等合成了高度致密的纳米结构的Mn-Zn铁氧体磁性纳米颗粒,采用高压场辅助烧结技术(HP-FAST)制备出了具有纳米结构的低损耗磁芯。
同时,添加剂是提高软磁铁氧体磁导率的有效途径。高磁导率铁氧体中,在一定范围内一般采用过量的Fe2O3和ZnO提高初始磁导率。适量的Nb2O5- WO3可以促进晶粒生长,提高初始磁导率。CaO- Bi2O3-MoO3-xNb2O5复合掺杂时,Mn-Zn铁氧体的综合电磁性能得到改善。少量的Nb2O5掺杂可以改善材料的微观结构,提高密度和频率稳定性。横店东磁集团研发的DMR50 系列铁氧体其工作频率能达到3 MHz,在f=500 kHz、B=50 mT、100 ℃条件下,损耗为80 kW/m3。
我国软磁铁氧体的产量从1975年的2500 t发展到2016年的约24万t,增长了约96倍,是当今世界第一大软磁铁氧体生产国,年产量占全球产量的50%以上。我国的铁氧体还有待进一步提高生产技术水平,缩短与国外的高牌号产品间的差距。
(五)金属磁粉芯
金属磁粉芯,也叫软磁复合材料,是由铁磁性粉末与绝缘介质混合经压制、烧结制备而成的一种复合材料。近年来,风力发电、光伏发电、新能源汽车行业、5G通讯等行业的发展对高性能金属磁粉芯的需求正快速增长。
工业上应用的软磁复合材料包括铁粉芯、铁硅粉芯、铁镍粉芯、铁硅硼粉芯、铁硅铝粉芯及坡莫合金粉芯等。该类粉末具有高饱和磁化强度和低矫顽力,通常采用气雾化法制备。中南大学软磁复合材料气雾化粉末制备技术成熟,气雾化FeSi、FeSiAl、FeNiMo、FeNi等球形粉末制备技术已扩展到国内多家大型企业。另一方面,磁性粉末的绝缘包覆处理在提高磁性粉末高频磁性能方面尤为重要。目前绝缘包覆剂研究较多的是粉末磷化,包覆SiO2、ZrO2、MgO、Al2O3等无机物。这些非磁性绝缘包覆层的存在虽可提高材料的电阻率、降低损耗,但是另一方面也降低了其磁导率。中南大学采用羰基铁粉(CIP)与还原铁粉(RIP)复合包覆SiO2,通过在SiO2网络状结构内复合ZrO2、铁氧体(MFe2O4)等方法,制备出CIP/SiO2-RIP/SiO2、CIP@SiO2@MFe2O4、CIP@SiO2-ZrO2、CIP@SiO2- ZrO2-CeO2等软磁复合材料,获得了高的磁导率和低的损耗,拓宽了该类材料的高频应用,为该类材料的进一步发展提供了有益的方向。
粉末冶金高温合金
粉末冶金高温合金是以镍为基体,添加有Co、Cr、W、Mo、Al、Ti、Nb、Ta等多种合金元素的一类具有优异的高温强度、抗疲劳和抗热腐蚀等综合性能的合金,是航空发动机涡轮轴、涡轮盘挡板、涡轮盘等关键热端部件的材料,加工主要涉及到粉末制备、热固结成型和热处理等过程。目前只有美国、俄罗斯、英国、法国、德国、中国等少数几个国家具备粉末冶金高温合金研发、生产的能力,其中美国、俄罗斯、英国处于领先的位置。目前,各国已着手设计开发使用温度达到815℃的第四代粉末高温合金。我国在粉末冶金高温合金领域起步较晚,在成分设计和工艺路线等方面主要参照欧美和俄罗斯等国的成功经验。从1977年开始,钢铁研究总院陆续引进、设计、制造了生产高温合金用的氩气雾化制粉装置、粉末处理设备、热等静压机、等温锻造机,于1980年年底基本上建成了一条较完备的粉末高温合金研制生产线。迄今,我国已研制出FGH91、FGH95、FGH96、FGH97、FGH98、FGH98I、FGH99和FGH100等牌号的粉末高温合金,取得了长足进步。在新型粉末高温合金的研发上,国内一些主要研究机构也紧随国际发展步伐,开展了第四代粉末高温合金成分设计等方面的工作。
(一)粉末高温合金成分
镍基粉末高温合金中涉及的元素种类繁多,高达十余种,表3所列为第四代典型粉末高温合金的化学成分。该类合金成分设计的主要目标是发展更高的强度、损伤容限、工作温度(约815 ℃) 以及更好高温组织稳定性。因此,四代粉末高温合金的各项性能对比大致如图3所示。对于涡轮盘用粉末高温合金,需要重点考虑不同元素对合金蠕变持久性能,室温和高温下的拉伸性能、疲劳性能,热加工性能、高温组织稳定性等因素的影响。伴随着相图计算技术的发 展,人们可以通过平衡相图计算的办法来实现对沉淀强化相的含量、固溶温度、硼化物和碳化物的含量、种类,以及有害相的析出量等的有效预测,避免了大量的合金制备和组织性能测试的时间。例如,RR1000的成功设计就是运用CALPHAD进行合金设计的成功例子。
图3 四代粉末冶金高温合金不同性能的综合对比
Fig. 3 Comprehensive properties of fourth generation powder metallurgy superalloys
(二)粉末高温合金的制备和组织调控
粉末高温合金的制备涉及到粉末的制备、粉末热固结成形、热机械变形、热处理等工艺过程,如图4所示,主要采用的加工路线有3种:① 制粉+热固结成型+热处理;② 制粉+热固结成型+热锻造+热处理;③ 制粉+热固结成型+热挤压+热锻造+热处理。
由于高温合金中往往含有Cr、Ti、Al 等难烧结元素,高温合金烧结通常要在高温高压环境中真空封装后才能进行。目前采用的高温合金粉末固结工艺有:真空热压成形、热等静压成形、热挤压、等温锻造等。其中,热等静压和热挤压工艺使用最为广泛。成形路线①也被称作直接热等静压成形(As-HIP),可以用来生产形状复杂的制件。然而,As-HIP工艺生产的涡轮盘往往具有较大的晶粒,并且还容易形成一种难以通过工艺控制去消除的冶金缺陷:原始粉末颗粒边界(Prior particle boundary, PPB),即一种在热固结过程中沿原始粉末颗粒表面析出的由碳化物、氧化物或碳氧化合物构成的网状组织。
原始粉末颗粒边界(PPB)是限制粉末高温合金直接热等静压成形广泛应用的主要因素。粉末的表面能是促使粉末表面碳化物、氧化物等脆性相形成的驱动力,因此在高温下快速闭合粉末间隙是降低PPB析出相数量的有效手段。通过两步HIP可以消除或减少PPB析出;粉末热处理可以使粉末内部的亚稳态碳化物变成稳定的MC和M23C6型碳化物,阻碍PPB析出相的出现。添加适量的除Ti以外的碳化物形成元素,如Ta、Nb、Hf等,能有效减少PPB析出物。轧制、挤压、锻造等热机械变形等工艺可以使合金内部产生较大的塑性形变,从而将HIP后合金内的PPB网破碎。
粉末高温合金的热机械变形包括热挤压、等温锻造等,主要目的在于改善合金的缺陷情况,获得均匀细小的晶粒。不连续动态再结晶是该类合金中热变形过程最重要的晶粒细化机制。针对高温合金的热加工变形工艺、组织的优化,通过制备梯度变形的试样研究变形参数与材料组织对应关系的高通量热变形方法也获得了广泛关注。
图4 粉末高温合金的三条主要制备路线
Fig. 4 Three major manufacturing routes of powder metallurgy superalloys
(三)粉末冶金高温合金的发展趋势
随着计算机技术的发展,基于大数据学习和人工智能对材料成分、工艺进行设计的方法已经在高分子、陶瓷等材料中得到了应用并取得成功。对于高温合金而言,由于公开的数据量少,成分、工艺、组织等变量多,一直很难通过上述办法进行有效的合金开发。然而,得益于高通量实验技术的发展,快速获得海量、可靠的成分−组织、组织−性能、工艺−性能等关系数据成为可能,这为开展机器学习打下了坚实的基础。
从工艺的角度上看,制备超纯净、高收得率的细粉是粉末制备工艺的一个重要发展方向。随着越来越多的工作聚焦于3D打印过程中致密化、裂纹、晶粒均匀性等方面的问题,采用增材制造的手段制备粉末高温合金制件也值得尝试。高性能航空发动机的涡轮盘在实际使用过程中,盘心与盘缘部位承受的温度、应力情况不同,通过可控的热处理工艺获得双性能涡轮盘是针对该涡轮盘复杂工况提出的有效手段,其中温度场的控制、晶粒和第二相的演变机理需要更深入的研究。此外,结合了组织模拟的工艺过程仿真是实现粉末高温合金涡轮盘从制粉、固结成型、热变形、热处理到最后机械加工成形过程一体化设计、优化的有效手段,需要进一步大力发展。
金属粉末增材制造(3D打印)
金属粉末增材制造可以分为粉末床激光增材制造(亦称选区激光熔化SLM)、粉末激光同轴送粉沉积(亦称激光熔覆沉积LCD,激光工程近净成形LENS)、粉末床电子束增材制造(亦称电子束选区熔化EBM)。美国“America Makes”、欧盟“Horizon 2020”和德国“INDUSTRIE 4.0”等均将增材制造列为提升国家竞争力的先进制造技术。我国也高度重视增材制造业的发展,发布实施《国家增材制造产业发展推进计划(2015−2016)》,并将其作为《中国制造2025》、《“十三五”国家战略性新兴产业发展规划》的重点发展领域。在增材制造工业应用方面,德国空客Airbus、波音Boeing等公司走在前列,已经将增材制造技术用于飞机零部件制造(见图5)。美国宇航局发起了金属3D打印技术在太空发射系统Space Launch System运载火箭的应用,欧洲航天局推出了涉及欧洲28个学术和工业合作伙伴名为AMAZE的3D打印研发项目。在我国,北京航空航天大学、西北工业大学、华中科技大学、南京航空航天大学、华南理工大学、西安交通大学、清华大学等较早地开展了金属增材制造相关基础研究,在工业化应用方面也各自取得了显著成绩。
图5 3D打印拓扑优化支架(图源airbus.com)和3D打印钛合金涡轮盖门铰链(图源castingssa.com)
Fig. 5 3D printing topology optimized bracket by Airbus (figure source airbus.com)(a), 3D printed titanium alloy turbo cover door hinge by Airbus (figure source castingssa.com)(b)
(一) 金属粉末增材制造材料
金属增材制造主要合金材料有铝合金、钛合金、铁基合金、高温合金、高熵合金、形状记忆合金等。
1 铝合金
激光增材制造铝合金研究主要聚焦于4xxx(Al-Si)系铝合金,也有部分文献报道了增材制造2xxx(Al-Cu)、5xxx(Al-Mg)和7xxxx(Al-Zn-Mg)系列铝合金。其中最成熟的体系属AlSi10Mg合金,强度约370 MPa、伸长率约6%。宋波等采用SLM打印了AlSi7Mg,揭示了激光快冷与组织性能之间的内在联系。在高强铝合金方面,空客子公司APWorks开发了3D打印专用Al-Mg-Sc合金,牌号为Scalmalloy,该合金打印件经时效后拉伸强度约520 MPa、伸长率约12%,APWorks采用该材料成形了仿生舱门,并与丰田公司开展合作。澳大利亚莫纳什大学吴鑫华院士团队研发了新型Al-Mn-Sc合金,其力学性能指标优于目前已报道的其他3D打印铝合金的。国内西工大、南航、华中科大、上海交大、中南大学也在“十三五”国家重点专项支持下开展了3D打印Al-Mg-Sc合金基础研究,性能指标与国际先进水平保持同步。中南大学粉末冶金国家重点实验室在3D打印铝合金粉末方面也取得重要进展,最大拉伸性能超520 MPa。国内工业应用方面,航空航天是3D打印高强铝应用的重点方向;中车工业也在布局3D打印高强铝在轨道交通上的应用,在粉末配方、力学性能和构件试用方面均取得重要进展(最大拉伸性能超520 MPa)。
2 钛合金
钛和钛合金由于具有优异的力学性能、耐腐蚀性能、生物相容性以及较低弹性模量而广泛应用于生物医用领域。增材制造技术为发展生物医用钛合金研究带来了新突破,引起了广泛的关注,包括以CP Ti为代表的α型钛合金,以Ti-6Al-4V为代表的α+β双相钛合金以及进几年兴起的以TiNb、TiTa基合金为代表的β型钛合金。其中,ATTAR等对选区激光熔化成形CP Ti进行了系统研究,制备的样品硬度261 HV、压缩强度(1136±15) MPa、压缩伸长率超50%,拉伸强度(757±12.5) MPa,拉伸伸长率接近20%[58]。林鑫团队利用高能激光沉积增材制造成形Ti-6Al-4V,获得了高伸长率(>18%),高强度((889±10) MPa),性能远超同类增材制造成形样品。在应用上,清华大学FANG 等研究了SLM成形Ti-6Al-4V合金孔隙度变化对骨组织支架性能的影响,获得了可以和各种松质骨、皮质骨的力学性能相对应的支架,弹性模量在3.7~5.7 GPa之间,屈服强度在27.1~84.7 MPa之间。
3 铁基合金
目前,铁基合金中用于3D打印的材料主要有304L、316L、17-4 PH和15-5 PH。NGUYEN等采用SLM制备了几乎完全致密的304L样品,并发现其微观结构包含纳米胞状晶和马氏体相。LIVERANI等采用SLM不同打印参数制备了316L样品,并在样品中发现三种缺陷:长条状缺陷、气孔、不规则孔隙。华中科技大学宋波等用SLM原位制备Cr3C2/Fe铁基复合材料,拉伸强度达1158 MPa,性能高于同类铁基复合材料,发展了SLM创造新材料的方向。
4 镍基高温合金
镍基高温合金在高温环境(800 ℃)下服役时具有高强度、优异的抗氧化和抗腐蚀性能,广泛应用于航空航天、国防工业等热端部件。传统成形工艺制备周期长且难以成形复杂结构零部件,而增材制造技术可兼具近净成形复杂精密结构和高温合金优良综合性能,成为研究热点。STRÖßNER等采用激光增材制造制备的IN718合金抗拉强度达1010 MPa、屈服737 MPa、伸长率20.6%;中南大学周科朝团队研究了激光成形IN718合金水平件和垂直件方向上的性能差异,打印态合金水平抗拉强度1110 MPa、屈服强度711 MPa、伸长率24.5%;垂直件抗拉强度1167 MPa、屈服强度858 MPa、伸长率21.5%;热处理后抗拉达1505 MPa、屈服强度1276 MPa、伸长率13.3%。
5 高熵合金
由于具有优异的力学性能、耐腐蚀性、高低温性能,高熵合金吸引了越来越多学者的关注。2015年,BRIF等首次利用粉末床3D打印设备制备了四元 等摩尔体系的FeCoCrNi高熵合金。中南大学刘咏团队研究了能量密度对选区激光熔化增材制造FeCoCrNiC0.5高熵合金的影响规律,制件最高拉伸强度达到749 MPa,远高于传统方法制备的高熵合金。李瑞迪等系统研究了选区激光熔化五元等摩尔体系的FeMnCoCrNi 高熵合金,并对其非平衡凝固的显微组织、物相组成、力学性能等进行了研究;有趣是在打印后的组织中发现了σ析出相,而传统方法所制备的FeMnCoCrNi体系的高熵合金都是单相FCC结构。同时,在打印后组织随着激光能量密度的增大而变得致密,并且打印后的样品中存在大量的位错以及纳米孪晶,通过位错的缠绕、堆积等可以增强其力学性能。
6 形状记忆合金
形状记忆合金成形加工一直是该合金的发展瓶颈,一方面,传统加工方法对形状记忆合金性能的控制工艺繁复,很难获得性能稳定的形状记忆合金;另一方面,形状记忆合金加工性能较差,传统工艺很难获得复杂结构的形状记忆合金器件,大量的拼接工艺使形状记忆合金价格高昂,极大限制了形状记忆合金的发展与应用。增材制造技术为形状记忆合金的制备带来了无限可能。基于层的三维构建技术可以赋予形状记忆合金更复杂的形状和结构,除此之外,灵活可控的参数调节可使合金获得不同的性能。国内外在3D打印NiTi基形状记忆合金方面开展了大量工作,有望在未来得到广泛应用。
(二)金属粉末增材制造的技术难题
1 热裂纹
增材制造成形过程合金熔池内高温度和应力梯度,导致打印件易出现热裂现象。未来解决增材制造热裂的方向有:热等静压处理来消除打印过程中产生的微裂纹;通过建模和实验研究应力产生规律,减小打印过程中的残余应力;通过微合金化改变凝固路径,以及晶粒细化,降低裂纹敏感性。
2 疲劳
工件的抗疲劳性能是工件能否得到广泛应用的重要指标。在增材制造过程中,通过高能激光束熔化粉末进行致密化,由于缺乏压力的作用,成形工件或多或少存在一定冶金缺陷,而这些冶金缺陷会在循环受力过程中造成应力集中。因此,相同材料增材制造成形样品的抗疲劳性能略低于锻造成形的样品,因为锻造成形的样品几乎全致密,冶金缺陷少。增材制造零件疲劳裂纹一般优先形核于内孔隙、表面孔隙及粗糙区域、内部凝固微裂纹处。因此增材制造疲劳性能改善成为该领域未来的重要研究方向。
3 金属粉末增材制造技术的发展趋势
影响增材制造产品质量主要有粉末原料、设备和工艺3个因素,未来前沿发展方向(不限于)有:新型专用合金粉末开发。目前适用于金属粉末增材制造的商用原材料粉末种类有限,制约了增材制造技术的拓展应用。匹配增材制造工艺新材料的开发,以及对现有粉末材料的改性,可显著提高增材制造产品质量。
大尺寸粉床直接成型系统。现有的金属粉末床增材制造系统主要针对小型精密零件(大多尺寸<300 mm),而面对大尺寸SLM成形结构时,结构的热变形、制造缺陷增多。需要从产品设计、材料、设备和工艺等方面入手解决。
4D打印技术(智能金属增材制造)。随着先进制造智能化的要求,4D打印的概念应运而生,4D打印指的是增材制造零件的形状或性能在外界环境刺激下能发生改变,而如何设计4D金属材料是未来前沿方向。
放电等离子烧结(SPS)
放电等离子烧结技术是利用石墨模具的上、下模冲和通电电极将直流脉冲电流和压制压力同时施加于粉末体,通过等离子活化和热塑变形,实现粉末体快速固结成形的烧结技术,又称等离子活化烧结、等离子辅助烧结。SPS技术的历史可追溯到20世纪30年代美国科学家提出的脉冲电流烧结原理。第一台工业型用SPS装置于1988年研发成功,并推广应用于新材料研究领域,SPS技术作为一种材料制备的新技术,引起了国内外材料学界的特别关注。SPS技术制备的材料体系包括:难熔金属、硬质合金、超高温陶瓷、复合材料、透明陶瓷、纳米结构材料、功能梯度材料、非稳态材料等。
(一)放电等离子烧结基本原理和特点
1 SPS烧结基本原理
SPS是低电压、直流电−交流电辅助、压力辅助烧结的合成技术。SPS系统主要由轴向压力装置、烧结模具、脉冲电流发生器和电阻加热设备组成。脉冲电流的主要作用是产生放电等离子体、放电冲击压力、焦耳热和电场扩散效应等。SPS烧结过程中,脉冲电流直接通过上、下模冲烧结粉体。在SPS烧结过程中,电极通入脉冲电流时产生放电等离子体,使得烧结体内部粉末颗粒均匀发热并促进颗粒表面活化,快速实现烧结致密化。SPS致密化可以看作在脉冲电流作用下,粉末颗粒间放电、通电产生焦耳热和加压的叠加作用结果。除加热和加压这两个烧结因素外,粉末颗粒之间的表面放电可促使局部产生高温,使表面局部熔化;高温等离子体溅射和放电冲击可有效去除粉末颗粒表面杂质(如表面氧化物等)和气体吸附,这些因素均能促进烧结过程。
2 SPS的原子扩散
扩散是粉末冶金烧结过程中粉体实现致密化的重要途径,原子的充分扩散是确保获得高密度粉末冶金制品的必要前提。与传统真空烧结、气氛烧结、热压、热等静压不同,放电等离子烧结引入了电场这一非热力学因素,能够显著促进原子的扩散。目前,国内外对于电场促进原子扩散机理研究已经取得了一定进展。基于典型阿伦尼乌斯关系的扩散系数方程,学术界对于电场促进原子扩散有两种主流解释:1) 电场提高了空位浓度,最终提高了原子跳进附近空位中的频率,进而提高了前指数D0,增大了扩散系数。2) 电场产生了“电子风力”效应,其减弱了粉末黏性流动的阻力,降低了原子扩散所需要的激活能QD,从而显著提高了扩散系数。
3 SPS的致密化
放电等离子烧结升温效率高,致密化速率快。SPS与热压类似,但产热及材料之间的传热方式有本质不同。如果坯体是导电材料,SPS的能量便会直接作用在样品及导电部件上,否则就必须借助模具产生的焦耳热并传至坯体。选用良好的模具材料可以实现低电压高电流电路,产生更充分的有效焦耳热,就算是烧结绝缘体粉末,热量也可以迅速有效的传递到样品,最大程度降低烧结时间及能量耗损。
放电等离子烧结可极大提高粉末的烧结效率。对于金属或合金体系,在合理的烧结参数下,通常仅需保温5 min便可获得相对密度超过99%的块体材料。其致密化机理主要包括晶界扩散、晶格扩散和黏性流动机制。在低温低压阶段,放电等离子烧结机理主要由晶界或晶界扩散等机制主导,在高温高压阶段,主要由位错攀移等机制主导。烧结机理转变温度与材料相关,原始粉末的形貌及颗粒尺寸也有一定的影响。放电等离子的快速致密化一直是研究的热点。早期学者认为电流可以击穿粉末表面,在烧结初期可以实现表面清洁作用,瞬时的强大电流可以产生等离子体来清除颗粒间的扩散屏障,例如氧化物等杂质,从而促进致密化,但等离子体的存在至今还未被证实。之后学者提出电迁移效应,认为电场可以促进导体材料中原子扩散,但这种效应在不同材料里得到的结论并不一致。近些年,学者们比较接受的电塑性理论,认为电场促进了位错运动,从而降低了流动应力,因此促进了致密化,这种理论也有待验证。
(二) 放电等离子烧结材料
SPS可以烧结的材料较为广泛,包括各种金属单质、合金、陶瓷、硬质合金与难熔金属等。从功能分类上,SPS可以烧结各种结构材料和功能材料。下面介绍几种SPS烧结的新材料。
1 功能梯度材料
功能梯度材料(FGM)的化学成分是梯度变化的,采用传统方法难以一次烧结完成。而CVD、PVD等沉积技术来制备梯度材料,成本高、效率低,难以实现规模化应用。通过调节SPS石墨模具中的温度场梯度,能够实现成分配比不同梯度材料的快速烧结致密化。目前采用SPS技术成功制备的梯度材料有:不锈钢/ZrO2、Ni/ZrO2、WC/Mo等梯度材料。其中,采用SPS技术制备的WC/Mo梯度材料的维氏硬度(HV)和断裂韧度分别达到了21 GPa和8 MPa·m1/2,显著降低了由于WC和Mo的热膨胀系数失配而导致的开裂。
2 铁电材料
SPS制备铁电材料主要是充分利用SPS技术低温、短时烧结的特点,实现对铁电材料的微结构调控。例如,采用SPS烧结铁电陶瓷PbTiO3时,在900~1000℃下烧结1~3 min,烧结后的铁电陶瓷平均颗粒尺寸<1 μm,相对密度超过98%。由于该方法制备的陶瓷中孔洞较少,因此在1×101~1×106 Hz之间介电常数基本不随频率变化。采用SPS制备铁电材料Bi4Ti3O12陶瓷时,在烧结过程中晶粒伸长和粗化的同时,陶瓷迅速致密化。用SPS技术容易获得晶粒取向度好的陶瓷材料,可观察到存在明显晶粒择优取向Bi4Ti3O12陶瓷的电性能有强烈各向异性。
3 磁性材料
采用SPS技术烧结磁性材料时具有烧结温度低、保温时间短的工艺优点。NdFeCoVB 在650 ℃下保温5 min,即可获得接近完全密实的块状磁体,而且晶粒不会发生明显长大。用SPS制备的Fe6Si4Al35Ni/MgFe2O4复合磁性材料(850 ℃,130 MPa)具有高的饱和磁化强度Bs=12 T和高的电阻率ρ=1×10 Ω·m。采用快速凝固法能够制备晶粒尺寸为几十纳米的软磁合金,但该方法难以获得合金块体,应用受到限制。目前采用SPS制备的块体磁性合金的磁性能已与非晶和纳米晶组织带材的软磁性能相当。
4 纳米材料
利用传统的热压烧结或热等静压等烧结方法来获取致密纳米材料时,难以兼顾纳米晶和全致密的技术要求。而SPS技术由于加热速度快、烧结时间短,可有效抑制晶粒长大。例如,用平均粒度为5 μm的 TiN粉末经SPS烧结(1963 K、196~382 MPa、5 min),可得到平均晶粒65 nm的TiN致密材料,结果证明SPS烧结可显著抑制晶粒粗化,制备的烧结体材料无疏松和明显的晶粒长大。
5 非晶合金
为制备大块非晶合金,采用非晶粉末在低于其晶化温度条件下进行温挤压、温轧、冲击(爆 炸)固化和等静压烧结等方法,仍存在不少技术难题,如非晶粉末的硬度总高于静态粉末,因而压制性能欠佳,难以发挥非晶态材料高强度的特点。SPS技术作为新一代烧结方法有望在这方面取得进展,如采用SPS技术制备的Mg-Ni-Si大块非晶态合金,相比A291D合金和纯镁金属,具有更高的腐蚀电位和更低的腐蚀电流密度。这是因为非晶化提高了镁合金的抗腐蚀抗力。
(三) SPS技术的发展趋势
根据2018年全球放电等离子烧结工业市场调研报告显示,截至2017年,以放电等离子烧结为代表的先进烧结技术市场的市值已达9亿1500万美元。报告同时指出,预计到2022年,放电等离子烧结等先进烧结技术市场占有份额将以每年6.6%的速度稳定增长,全球市值将于2022年底扩大到13亿美元(数据来源bccresearch.com)。未来,放电等离子烧结将不断扩大其在核能材料、航空航天陶瓷热障材料、先进钛合金材料、梯度复合材料等高端材料市场的应用。
SPS的致密化理论目前尚不完全明晰,其机理突破是发展新型电场快速烧结的基础,需针对不同材料体系进行系统的实践与理论研究来完善,为SPS技术和设备改进提供理论指导。未来研究的重点方向(不限于)如下。
1) 由于SPS烧结炉采用低电压、高电流的通电模式,由于功率限制,SPS技术难以制备大尺寸(>200 mm)的产品。因此,SPS技术需要增加设备的多功能性和脉冲电流的容量,以生产尺寸更大的产品。
2) 开发全自动化的SPS烧结系统,以满足形状复杂、性能优异的产品和三维梯度功能材料的生产需要。
3) 需要开发适合于SPS技术的粉末原材料,并研制比常规石墨材料强度更高、重复使用率更好的新型模具材料,以提高模具的承载能力并降低模具消耗费用。
4) 需要建立模具温度和工件实际温度的温差关系,以便更好的控制产品质量,并形成相应的技术标准。
5) 外场辅助的SPS技术,如增加脉冲压力的功能,揭示脉冲加压作用下SPS致密化机理及组织演化规律。
总结
新中国成立70周年以来,我国粉末冶金材料和技术得到了快速发展,材料体系、成形技术、工艺装备、技术水平、粉末冶金制品的市场份额等均提升明显。在粉末冶金新材料,包括铁基粉末冶金材料、硬质合金、磁性材料、镍基粉末冶金高温合金,以及粉末冶金新型成形技术,包括粉末增材制造、放电等离子烧结和热等静压技术等方面均呈现出崭新局面。同时,新型相图计算、有限元方法、第一性原理计算等理论计算方法为粉末冶金材料和技术的发展注入了新鲜的血液。